AI's Geometric Deep Learning Speeds Car Design from Months to Hours.
Unlock the future of auto design: AI's geometric deep learning slashes simulation times, powering unprecedented innovation and efficiency.
July 11, 2025
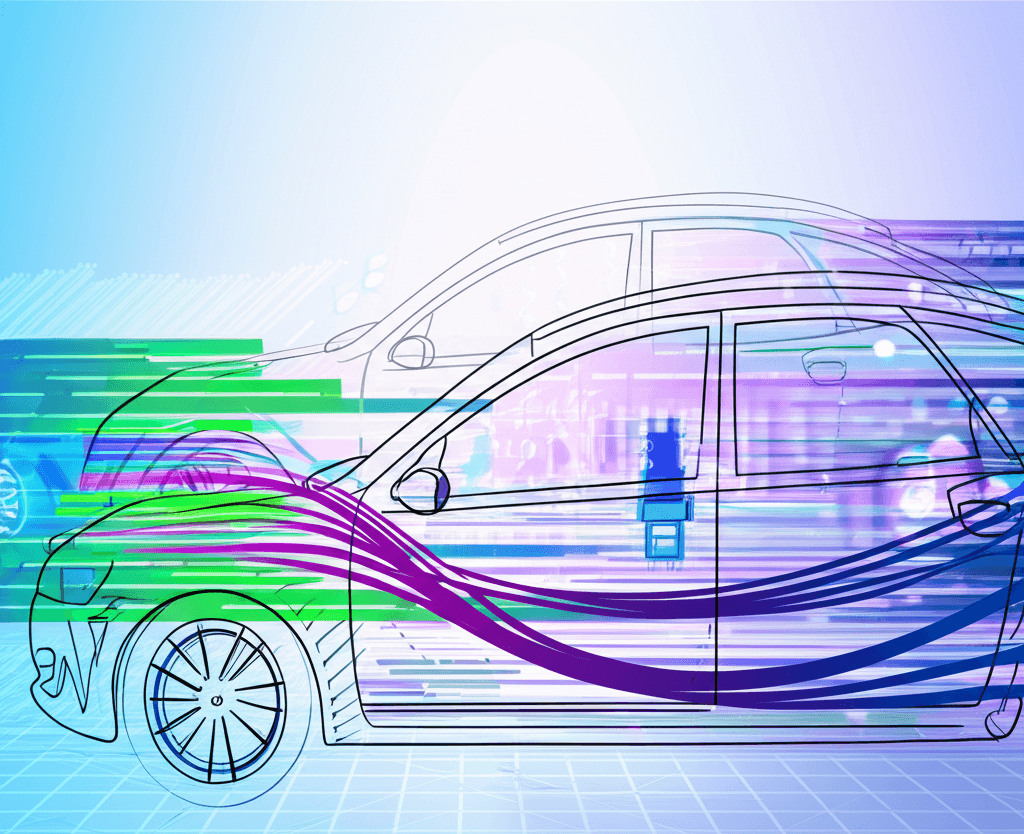
A paradigm shift is underway in automotive engineering, where artificial intelligence, specifically a branch known as geometric deep learning, is dramatically accelerating research and development. Companies like Altair are at the forefront of this transformation, leveraging AI to compress design and simulation timelines from weeks or even months to a matter of days or hours.[1][2] This is not merely an incremental improvement; it represents a fundamental change in how vehicles are designed, tested, and brought to market, with significant implications for innovation, safety, and efficiency in the auto industry. The core of this revolution lies in teaching AI to understand the language of physics and geometry, enabling it to predict real-world performance with astonishing speed and accuracy.
Geometric deep learning is a specialized field of AI that, in simple terms, gives neural networks the ability to understand and interpret 3D shapes and their physical properties.[3] Coined in 2016 by Professor Michael Bronstein, this technology moves beyond traditional machine learning, which often relies on structured, parametric data.[3] Instead, it can learn directly from the complex, non-parametric geometries found in computer-aided design (CAD) and computer-aided engineering (CAE) models.[3][4] This is a crucial distinction for automotive engineering, where designs are often organic and intricate. By training on historical simulation data—for example, the results of thousands of previous crash tests or aerodynamic analyses—the AI learns the intricate relationship between a component's shape and its performance under various physical stresses.[5][3] This allows engineers to bypass the time-consuming process of running new, high-fidelity simulations for every design tweak. A full vehicle crash simulation, for instance, can take 24 hours to run on a high-performance computer.[2] With a trained geometric deep learning model, a prediction for a modified design can be generated in seconds or minutes.[2][6]
Altair, a major player in engineering software, has operationalized this technology through its Altair PhysicsAI platform.[5][3] This tool integrates into existing CAE workflows, allowing engineers to train models on their own historical simulation data, regardless of its source.[1] Once trained, these AI models can deliver physics predictions up to 1,000 times faster than traditional solvers.[5][3][1] This radical speed-up empowers engineering teams to explore a vastly wider range of design alternatives early in the development cycle.[7][1] Instead of meticulously selecting a few promising candidates for lengthy simulation, designers can test numerous variations, leading to more optimized and innovative outcomes.[2] This could involve anything from tweaking the shape of a side mirror to reduce drag and improve fuel efficiency to redesigning a chassis component for better crash performance.[6] The technology isn't limited to a single domain, showing applicability across structural analysis, computational fluid dynamics (CFD), electromagnetics, and more.[6]
The implications of this AI-driven approach for the automotive industry are profound and far-reaching. The most immediate benefit is a drastic reduction in product development timelines.[8][9] What once took months of iterative design and testing can now be accomplished in days, allowing automakers to bring new models and technologies to market much faster.[1][10] This agility is critical in a rapidly evolving market, especially with the race towards electrification and autonomous driving.[11][12] Beyond speed, the ability to conduct more extensive design exploration leads to better products. Engineers can optimize for multiple attributes simultaneously—such as weight reduction, safety, and manufacturing cost—with a level of insight that was previously unattainable.[9][13] This helps in creating lighter, more fuel-efficient, and safer vehicles. Furthermore, by "frontloading" simulation into the early design stages, companies can identify and rectify potential flaws before costly physical prototypes are even built, leading to significant cost savings.[13][4] The technology also acts as a "design co-pilot," augmenting the capabilities of human engineers rather than replacing them, freeing them from repetitive tasks to focus on innovation and strategic decisions.[10]
In conclusion, the integration of geometric deep learning into automotive engineering marks a pivotal moment for the industry. By empowering engineers with AI tools that can rapidly predict physical performance, companies like Altair are enabling a new era of accelerated innovation. This shift from a slow, sequential process of design and validation to a rapid, AI-informed exploration of possibilities promises to deliver safer, more efficient, and more advanced vehicles to consumers faster than ever before. As this technology becomes more widespread, it is set to become a standard, indispensable tool in the automotive engineer's arsenal, fundamentally reshaping the competitive landscape and driving the future of mobility.[10][3] The ability to learn from past data and predict the future performance of complex 3D designs is not just speeding up a process; it is making the entire endeavor of automotive engineering smarter and more effective.